Process improvement methodologies
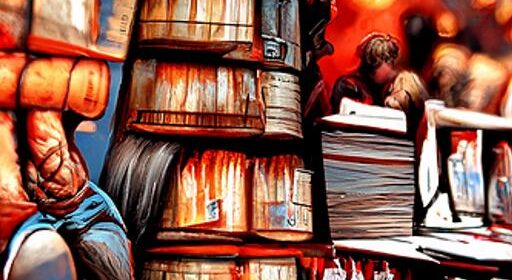
It can also be referred to as lean production or just-in-time production. It identifies all process bottlenecks and improves those bottlenecks or restrictions until they are removed. According to this model, it is considered optimized if a process causes less than 3.4 errors per million cycles. For example, Mitsubishi Heavy Industries America (MHIA) initially designed custom-made (design-to-order) chemical plant designs for the environmental compatibility of 26%.
Total quality management (TQM) is a customer-focused methodology that includes continuous improvement over time. The company finally established a standardized module package that reduced errors in the design phase and customer costs by 5 to 10 percent. This process improvement method lets you quickly embed constructive criticism and feedback deep into your corporate culture. Intel, for example, has introduced lean manufacturing technology to deliver higher-quality processors within a shorter time frame.
However, after introducing the principles of the Kaizen methodology, the company made small, continuous changes to its design process to create a standardized package of modules. This process improvement method lets you quickly embed constructive criticism and feedback deep into your corporate culture. This resulted in fewer errors in the design phase and reduced costs for the customer by 5 to 10%. Although the name suggests that this method is specific to the manufacturing sector, its core principle can also be applied to other industries.
Given the significant benefits of process improvement, it’s essential to understand which methodology meets your business needs and to have an implementation plan ready. The Theory of Constraints methodology is highly focused on achieving rapid improvements. Six Sigma is a well-known technique for reducing variability and defects to less than 3.4 per 1 million units. Applying the 5S method promotes safety, reduces costs, and increases team efficiency by avoiding waste from production processes..
According to research, over 40% of employees spend at least a quarter of their week on manual, repetitive tasks such as email, data collection, and data entry. Toyota executives invented this concept to adapt quickly and efficiently to changing demand for models and reduce losses by keeping immediately needed inventory in-store. Another benefit is that it helps standardize and makes process improvement more consistent. Mitsubishi Heavy Industries America (MHIA) used the principles of the Kaizen Method to make small, continuous changes in its design process.
MicroMetl, a Nevada-based heating and air conditioning equipment manufacturer, analyzed its workflows to improve product quality and consistency. For example, the American multinational company General Electric had difficulty improving the service quality of its product by %26, even after hiring experienced professionals. It’s a straightforward way to thoroughly analyze your processes and recommend improvements by simply asking “why” five times until you figure out the problem is.. 5-whys analysis is another well-known process improvement technique that focuses on identifying and resolving the root cause of a problem.
Total Quality Management (TQM) · It can also be called lean production or just-in-time production. Total Quality Management (TQM) · Within Six Sigma, process engineers use two sub-methods: DMAIC to improve existing processes and DMADV to create new techniques. Again, there is a lot of overlap between these different process improvement methods regarding the diagrams they use for analysis. It includes team feedback that highlights issues and successes to make further improvements.
Again, there is a lot of overlap between these different process improvement methods regarding the diagrams used for analysis. The Toyota production system, just-in-time manufacturing, aims to minimize inventory costs and increase efficiency by producing goods following requirements. To use this technique effectively, the process improvement team must map the value stream to understand buyers’ perceptions. In this way, teams can successfully avoid waste and redundancy in business processes. However, after integrating Six Sigma, they streamlined their functions, which resulted in higher sales.
Root cause analysis is another critical process improvement method that helps you fully understand the causative factors and underlying issues behind the most prominent business issues you face daily. By applying lean process improvements, the company reduced indirect labor costs by 21 percent, which helped to reduce prices further and increase market share. Kanbanize is an excellent software tool that processes managers and supervisors can use to implement the Kanban process improvement methodology. By implementing a technological change or a custom application, these repetitive tasks can be automated, and employees can dedicate time to core aspects of their work.
It aims to minimize errors and maximize value across industries by using data and statistics. One notable aspect is that companies miss the first three steps and go straight to the improvement or design phase, leading to project failure. Instead of defining the project with strict deadlines, an agile approach requires more iterations. This form of process improvement has many names, with lean manufacturing being the most common.
Process improvement is a powerful tool for improving a company’s performance and can be achieved with the proper process improvement methods. Process improvement is a powerful tool for enhancing a company’s performance and can be achieved with the appropriate process improvement methods. An agile methodology improves communication and collaboration between stakeholders and makes it easier to adapt to change. Lean manufacturing aims to reduce costs by avoiding waste.
As part of this methodology, process engineers use two techniques DMAIC (define, measure, analyze, improve %26 control) and DMADV (define, measure, analyze, design %26 verify), to achieve the desired results. Six Sigma uses data and statistics to minimize the number of variations within the end product. Business process improvements are methods that a team uses to assess and adjust its current processes to increase profitability. This technique is often used in supply chain management and customer satisfaction projects.
Womack, Daniel Jones, and Daniel Roos highlight five main principles in the book “The Machine That Changed the World,” based on the authors’ experiences in Toyota manufacturing. However, each process improvement method offers a unique set of tools that easily complement the others. If you’re facing operational challenges, receiving customer complaints, or want to streamline existing processes, it’s time to implement process improvement methods. As part of Lean and Kaizen methodologies, the 5S model helps you implement continuous and rapid improvements.
By implementing quality control factors and waste reduction techniques, Intel reduced the time to get a microchip to the factory from more than three months to less than ten days. Here are 10 of the best techniques to kick-start your process improvement initiative.
Lean process improvement
We can define Lean as a system for continuously developing process improvements that focus on reducing and eliminating waste. LEAN is more than a set of techniques. It is a mindset of continuous improvement in the quest for perfection. Although Lean and Six Sigma have been taught as separate methods for many years, the line is blurred, and it is now standard practice to combine Lean and Six Sigma teachings as Lean Six Sigma to get the best of both worlds.. Once you’ve mapped your process on a Kanban board, you can start analyzing the value-adding and non-value-adding activities in your workflow..
At its core, lean is a popular approach to streamlining manufacturing and transactional processes by eliminating waste and streamlining operations while continuing to provide customers with added value.. By continuously removing these causes of poor quality, the LEAN mentality strives endlessly to create the perfect process. Lean process improvement aims to enable teams to systematically find ways to deliver more value to their customers faster.. By configuring and monitoring your workflow’s cycle time (the time a work item was actively processed), you can measure how long it takes for work to be completed and then analyze the slow stages of your process.
Another way to improve lean processes that allow you to meet customer demand most efficiently is Heijunka. It aims to optimize your processes, divide large amounts of work into smaller portions, and organize team capacity as needed. The entire process consists of identifying opportunities for improvement, implementing changes, and measuring the affected changes. LEAN manufacturing techniques began to identify and reduce wasteful operating practices systematically.
Lean Six Sigma offers a systematic approach and a combined toolkit to help employees build problem-solving skills. What is often not emphasized is that both companies’ change initiatives led to incredible business results when they combined Lean Six Sigma with organizational development techniques.. From coaching executives on strategy development, implementation, and direction to engaging employees to create a problem-solving culture and everything in between—learn how lean thinking and practice can improve your organization’s performance. This is not always easy in manufacturing, as different raw materials are processed by other machines, people, and processes.
This allows you to identify process bottlenecks and focus your improvement efforts on reducing delivery time and increasing productivity. To support organizational change, organizational development practitioners must understand how corporate systems and processes are driven by complex factors such as behavior and cultural norms. Efficient operations coordinate various resources in the best possible order to deliver a product or service. This is done through a systematic, scientific approach to practice continuous improvement as part of daily work..
Continuous process improvement
Continuous improvement, sometimes called continuous improvement, is the constant improvement of products, services, or processes through incremental and groundbreaking enhancements. Before you begin an ongoing improvement process, it’s best to analyze what resources you will likely need. The Continuous Improvement Process (CIP) is a constant effort to improve products, services, or processes. In lean methodology, continuous improvement aims to improve every function in your organization by enhancing the activities that generate the most value for your customer while avoiding as many wasted activities as possible.
Improved product quality One of the main goals of any continuous improvement process is identifying opportunities for change. The continuous improvement process (CIP) is a constant effort to improve products, services, or processes. Continuous improvement events can take one to five days, depending on the topic’s depth and breadth. Team members are usually given “tasks” that help the new processes take hold in the company and may take some time to complete. Enabling Transformation with Continuous Improvement (PDF) Sheila Shaffie and her team from ProcessArc, a customer experience architecture firm, explain why using multiple complementary methods for business transformation and continuous improvement is beneficial.
We’ve already addressed the benefits of Continuous Improvement, and now it’s time to take a closer look at why and how the right processes will result in exponential benefits. See how AgilePlace supports continuous delivery initiatives, reduces waste, and improves delivery processes and your team’s speed. A continuous improvement process often called a continuous improvement process, is a continuous effort to improve products, services, or processes. It is a six-stage systematic approach for planning, sequencing, and implementing improvement measures based on data and explanations of the Shewhart cycle (Plan, Do, Study Act).
However, a continuous improvement process has the added benefit of pointing out the areas where you might be throwing money out the window. The CIP provides a common language and methodology that enable the improvement process to be understood. Less was increasing overall efficiency is preventing and eliminating waste at the core of continuous improvement processes. Implementing and maintaining continuous improvement processes is hard work that requires a lot of commitment, good leadership, and the right corporate culture.
Setting performance expectations is a key to continuous improvement, as the accuracy of objectives and completeness is an essential parts of the improvement process.
Process improvement methods
Changing from one day to the next can lead to many errors or problems that delay the implementation of process improvement methods. If you can’t find a one-size-fits-all solution to all issues immediately, consider combining different process improvement methods to create something unique and suitable for your company. It is based on DMAIC and combines the tools from both process improvement methods, such as value stream maps and SIPOC analysis diagrams.. Now that you know the best process improvement methods, start experimenting with your business processes and putting the techniques into practice.
Remember that there is a lot of overlap between these different methods of improving business processes regarding the diagrams they use to analyze strategies. To use this technique effectively, the process improvement team must map the value stream to understand buyers’ perceptions. In this way, teams can successfully avoid waste and redundancy in business processes. For this reason, many companies use process improvement methods to adapt their operations to customer requirements… Business process improvements are ways a team uses to assess and adjust its current processes to increase productivity, streamline workflows, adapt to changing business needs, or increase profitability.
The key is to innovatively use the strengths of each process improvement method and apply them according to the fundamental needs of the process. Standard think tank or team brainstorming sessions provide multiple benefits to any organization that adheres to a specific process improvement method. It’s a straightforward way to thoroughly analyze your processes and recommend improvements by asking “why” five times until you figure out the problem is. That’s why you need to know the best process improvement methods that work for your organization and effectively produce the results you want.
The fact that it helps standardize and makes process improvement more consistent is another benefit. This process improvement method focuses primarily on increasing productivity, quality, and efficiency through corporate culture or daily work to cultivate a culture that does not punish mistakes or errors but prevents them from happening again. In the book The Machine That Changed the World, Lean, Womack, Daniel Jones, and Daniel Roos highlight five main principles based on the authors’ experiences in making Toyota.
Improving business processes
Remember that there is a lot of overlap between these different methods of improving business processes regarding the diagrams they use to analyze strategies. Process improvement includes identifying, analyzing, and improving existing business processes to optimize performance, meet best practice standards, or improve quality and user experience for customers and end users. Business process improvement (BPI) is a practice in which business leaders analyze their business processes to identify areas where they can improve. Improving business processes is a skill that companies and their employees can work to strengthen over time.
Diagrams make it easy to visualize and understand how a restriction affects other parts of the process and where it can be reduced.. It is based on DMAIC and combines the tools from process improvement methods, such as value stream maps and SIPOC analysis diagrams. Since process improvement is an overarching business term rather than a job title, several titles fall under process improvement. Although this technique for improving business processes was initially designed to maintain a clean physical workplace, it can also be used to support an organized and orderly virtual workplace.
In addition to these and other process improvement techniques, business leaders and managers typically use various tools to understand and get an overview of their business processes. It redesigns existing business tasks, improves their effectiveness, improves the workflows involved, and optimizes performance. There are lots of different ways to improve business processes, but the basic idea is usually the same: Take your old methods and look for ways to improve them. You can also use various tools to enhance business processes—the five whys as a framework for looking for inefficiencies or problems.
Improving business processes can speed up development and lead to higher product quality. Again, ensure you include everyone following the process in the discussion, as they’ll be able to provide first-hand perspectives to guide your business process improvement activities. It is a specific framework designed to advise the company on improving business processes. We’ve covered six essential methods for process improvement, but there are many more methods and a host of additional ways that match Six Sigma, Lean, and TQM.
While “business process improvement” can describe any process improvement activity in a company, a few specific techniques can be used to formally practice process improvement in a business context. Any business process can be improved, from the most strategically important to the most mundane. A lean approach at Six Sigma helps you avoid waste in your company and reduce process errors.
References:
- https://www.lucidchart.com/blog/process-improvement-methodologies
- Process Improvement Methodologies – Complete List [6+ Tools] – Tallyfy
Related Posts
It can also be referred to as lean production or just-in-time production. It identifies all process bottlenecks and improves those bottlenecks or restrictions until they are removed. According to this model, it is considered optimized if a process causes less than 3.4 errors per million cycles. For example, Mitsubishi Heavy Industries America (MHIA) initially designed…
Business Consulting Articles
- About cookies and cookie consent
- Advisory Consulting
- Business Growth Consulting | Unlocking Your Business Potential
- Business Process Consulting Services Can Improve Your Business
- Organizational Development Consultant
- Privacy Policy
- Strategic Advisory Services Explained: A Comprehensive Guide
- Top 100 Advisory Consulting Terminology
- Top 100 AI as a Service (AIaaS) Terminology
- Top 100 Business Consulting Terminology
- Top 100 Executive Coaching Terminology
- Top 100 Operation Management Terminology
- Top Advisory Consulting Terminology
- Top AI as a Service (AIaaS) Terminology
- Top Business Consulting Terminology
- Top Executive Coaching Terminology
- Top Operation Management Terminology
- AI Generated Q&As
- Benefits of advisory consulting
- Blog
- Boutique Firms
- Budgeting
- Business advisory consulting
- Business Consulting
- Business consulting services
- Business Management
- Business planning
- Case studies on specific industries
- CEO
- CFO
- Change management
- CIO
- Client success stories
- CMO
- Collaboration and partnerships
- Consulting
- COO
- Creative thinking
- Critical thinking skills
- Culture and values
- Executive Coaching
- Expert guidance and insights
- Financial advisory consulting
- Financial analysis
- Financial consulting
- Financial Consulting
- Financial consulting services
- Financial strategies
- Fractional Executive
- Goal setting
- Human Resource Management
- Increased efficiency and profitability
- Industry knowledge and experience
- Insight
- Investing
- IT Consulting
- Leadership and management
- Leadership styles
- Management Consulting
- Management Consulting
- Market analysis
- Market analysis
- Marketing consulting
- Marketing strategies
- Marketing strategies
- Methodologies
- Operational strategies
- Organizational structure
- Process improvement
- Professional qualifications and certifications
- Retirement planning
- Risk analysis
- Risk management and compliance
- Sales techniques
- Scaling and expansion
- Strategic consulting
- Strategic foresight
- Team diversity and collaboration
- Technology advisory consulting
- Technology consulting services
- Technology solutions
- Testimonials from satisfied clients
- Tier 1 Firms
- Tier 2 Firms
- Vision and direction
- What is Advisory?
- What is Consulting?