Understanding Six Sigma Methodology: A Strategic Solution for Process Improvement
by Consultant
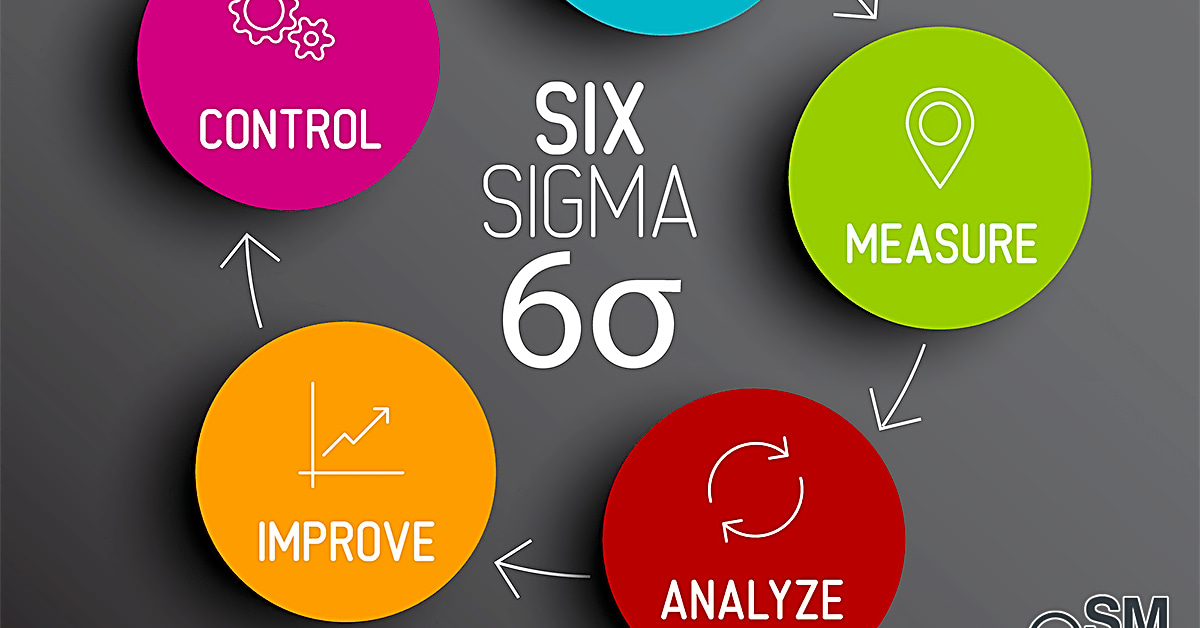
The Six Sigma methodology has become a popular and effective approach for process improvement in various industries. It is a data-driven methodology that aims to identify and eliminate defects or errors in a process, ultimately leading to improved efficiency and quality. Originating from Motorola in the 1980s, Six Sigma has now been adopted by companies worldwide, including Fortune 500 companies like General Electric and Toyota.
This article will delve into the key aspects of Six Sigma methodology and its role as a strategic solution for process improvement. Whether you are new to Six Sigma or looking to deepen your understanding, this article will provide you with valuable insights and practical knowledge.
We will start by exploring the fundamentals of Six Sigma, including its principles, tools, and techniques. Then, we will examine how Six Sigma can be integrated into a company’s overall strategic solutions, specifically in the context of process improvement. Finally, we will cover some real-world examples of how Six Sigma has been successfully implemented in various industries.
Whether you are a business owner, manager, or simply interested in learning more about Six Sigma, this article is for you. So let’s dive in and uncover the power of Six Sigma methodology as a strategic solution for process improvement.
Are you looking for ways to improve your business strategy? Are you seeking guidance from management consultants? Look no further than Six Sigma methodology. In this article, we will explore everything you need to know about Six Sigma and how it can help you achieve your strategic goals. Six Sigma is a data-driven methodology that focuses on process improvement and reducing defects or errors in a company’s processes. It was originally developed by Motorola in the 1980s and has since been adopted by many organizations worldwide. The goal of Six Sigma is to improve the quality of products and services by identifying and eliminating variations or defects in processes. Now, let’s dive into the key principles and methodologies of Six Sigma. The most commonly used approach is DMAIC, which stands for Define, Measure, Analyze, Improve, and Control. This five-step process is used to identify the root cause of a problem and implement solutions to improve the process. Another approach is DMADV, which stands for Define, Measure, Analyze, Design, and Verify. This methodology is used when creating a new process or product to ensure it meets customer requirements and is free of defects. Six Sigma also offers different levels of certification, including Yellow Belt, Green Belt, Black Belt, and Master Black Belt. These certifications provide individuals with the necessary skills and knowledge to effectively implement Six Sigma methodologies in their organization. Implementing Six Sigma requires strong leadership from top-level management. Leaders must be committed to the process and actively involved in driving change within the organization. Additionally, data-driven decision making is crucial in Six Sigma methodology. It involves collecting and analyzing data to make informed decisions rather than relying on intuition or guesswork. This allows for a more objective and efficient approach to problem-solving. In conclusion, Six Sigma methodology is a strategic solution for process improvement that can benefit any organization. It helps identify and eliminate defects in processes, leading to improved quality and efficiency. To learn more about Six Sigma, check out the resources provided below. Remember, with Six Sigma, the possibilities for improvement are endless.
The Benefits of Six Sigma Certification
use HTML structure with Six Sigma certification only for main keywords and
for paragraphs, do not use “newline character”
The Basics of Six Sigma
Six Sigma methodology is a data-driven approach to process improvement that has been widely adopted by businesses around the world. But where did it come from, and what are its underlying principles?
The origins of Six Sigma can be traced back to the 1980s when Motorola developed the concept as a way to measure defects in their manufacturing processes. In the 1990s, it was further refined and popularized by Jack Welch, the CEO of General Electric at the time.
The core principle of Six Sigma is to reduce variation in processes and eliminate defects, ultimately leading to increased efficiency and improved quality. It is based on the idea that any process can be measured, analyzed, and improved upon using data and statistical methods.
One of the key aspects of Six Sigma is its focus on customer satisfaction. By reducing defects and improving quality, businesses can ensure that their customers are receiving products and services that meet or exceed their expectations. This not only leads to higher customer satisfaction but also helps build a strong reputation for the company.
Another key principle is the use of DMAIC (Define, Measure, Analyze, Improve, Control) as a structured problem-solving approach. This method allows businesses to identify issues, gather data, analyze it, implement solutions, and then monitor and control processes to sustain improvements.
Overall, understanding the origins and principles of Six Sigma is crucial to implementing it effectively within a business. By following its structured approach and focusing on customer satisfaction, companies can achieve significant process improvements and strategic goals.
Leadership and Data-Driven Decision Making
Six Sigma methodology is a proven strategy for process improvement, and leadership plays a crucial role in its success. The success of Six Sigma implementation depends on the commitment and support of top-level management. It is the responsibility of leaders to create a culture of continuous improvement and data-driven decision making within the organization.
Effective leaders understand the importance of using data to drive decision making. With Six Sigma, data is collected and analyzed to identify areas for improvement and make informed decisions. This ensures that decisions are not based on guesswork or personal opinions, but on solid data and facts.
Leaders also play a key role in creating a sense of urgency for implementing Six Sigma. They must communicate the benefits of this methodology to their team and show their commitment by being actively involved in the process. This involvement and support from leadership helps to overcome any resistance or skepticism from employees, ensuring a smoother and more successful implementation.
In addition, leaders are responsible for setting clear goals and expectations for the Six Sigma project. This includes defining the scope, timeline, and desired outcomes. By setting measurable goals, leaders can track progress and ensure that the project stays on track.
Overall, leadership is essential for driving success with Six Sigma. With their support and guidance, organizations can achieve their strategic goals and see significant improvements in their processes.
Applying Six Sigma Methodology
When it comes to improving processes within a business, the Six Sigma methodology has proven to be a strategic solution. This approach, developed by Motorola in the 1980s, focuses on identifying and eliminating defects in a process to improve efficiency and quality. It involves using data-driven techniques and statistical analysis to identify areas for improvement and make informed decisions.
The Six Sigma methodology is based on two key methodologies: DMAIC (Define, Measure, Analyze, Improve, Control) and DMADV (Define, Measure, Analyze, Design, Verify). Both of these methodologies follow a structured approach to process improvement, with DMAIC used for existing processes and DMADV for designing new processes.
DMAIC for Process Improvement
The DMAIC approach is ideal for improving existing processes that are not meeting quality standards or are experiencing problems. The first step is to define the problem or goal of the process improvement. This involves understanding the current state of the process and setting achievable goals for improvement.
Next, data is collected and analyzed to measure the current performance of the process. This includes identifying any areas of waste or inefficiency.
After analyzing the data, solutions are developed and implemented to improve the process. These solutions may include streamlining processes, eliminating waste, or implementing new technology.
Finally, controls are put in place to ensure that the improvements are sustained over time. This involves monitoring and continuously measuring the process to make sure it remains efficient and effective.
DMADV for Process Design
The DMADV approach is used when designing new processes or products. The first step is to define the goals and objectives of the new process or product.
Next, data is gathered and analyzed to determine the best design for the process or product. This involves identifying customer needs and preferences and developing a design that meets those needs.
After designing the process, it is verified through testing and simulations to ensure it will meet the desired goals. Once verified, the process is implemented and continuously monitored to ensure it remains effective.
In conclusion, implementing Six Sigma methodology through DMAIC or DMADV can greatly benefit a business by improving processes and achieving strategic goals. By following a structured approach to process improvement, businesses can streamline their operations and increase efficiency and quality.
In conclusion, Six Sigma methodology offers a comprehensive approach to process improvement and strategic planning. With its origins in manufacturing but now applied in various industries, Six Sigma can help organizations achieve their goals through data-driven decision making and continuous improvement. Whether you are a business owner or a management consultant, understanding Six Sigma can greatly benefit your business strategy and overall success. We hope this article has provided you with valuable insights and resources to further your understanding of Six Sigma.
Related Posts
Learn about strategic planning, organizational strategy, and effective strategic solutions with Six Sigma methodology. Discover resources for strategic analysis, thinking, and leadership.
Business Consulting Articles
- About cookies and cookie consent
- Advisory Consulting
- Business Growth Consulting | Unlocking Your Business Potential
- Business Process Consulting Services Can Improve Your Business
- Organizational Development Consultant
- Privacy Policy
- Strategic Advisory Services Explained: A Comprehensive Guide
- Top 100 Advisory Consulting Terminology
- Top 100 AI as a Service (AIaaS) Terminology
- Top 100 Business Consulting Terminology
- Top 100 Executive Coaching Terminology
- Top 100 Operation Management Terminology
- Top Advisory Consulting Terminology
- Top AI as a Service (AIaaS) Terminology
- Top Business Consulting Terminology
- Top Executive Coaching Terminology
- Top Operation Management Terminology
- AI Generated Q&As
- Benefits of advisory consulting
- Blog
- Boutique Firms
- Budgeting
- Business advisory consulting
- Business Consulting
- Business consulting services
- Business Management
- Business planning
- Case studies on specific industries
- CEO
- CFO
- Change management
- CIO
- Client success stories
- CMO
- Collaboration and partnerships
- Consulting
- COO
- Creative thinking
- Critical thinking skills
- Culture and values
- Executive Coaching
- Expert guidance and insights
- Financial advisory consulting
- Financial analysis
- Financial consulting
- Financial Consulting
- Financial consulting services
- Financial strategies
- Fractional Executive
- Goal setting
- Human Resource Management
- Increased efficiency and profitability
- Industry knowledge and experience
- Insight
- Investing
- IT Consulting
- Leadership and management
- Leadership styles
- Management Consulting
- Management Consulting
- Market analysis
- Market analysis
- Marketing consulting
- Marketing strategies
- Marketing strategies
- Methodologies
- Operational strategies
- Organizational structure
- Process improvement
- Professional qualifications and certifications
- Retirement planning
- Risk analysis
- Risk management and compliance
- Sales techniques
- Scaling and expansion
- Strategic consulting
- Strategic foresight
- Team diversity and collaboration
- Technology advisory consulting
- Technology consulting services
- Technology solutions
- Testimonials from satisfied clients
- Tier 1 Firms
- Tier 2 Firms
- Vision and direction
- What is Advisory?
- What is Consulting?